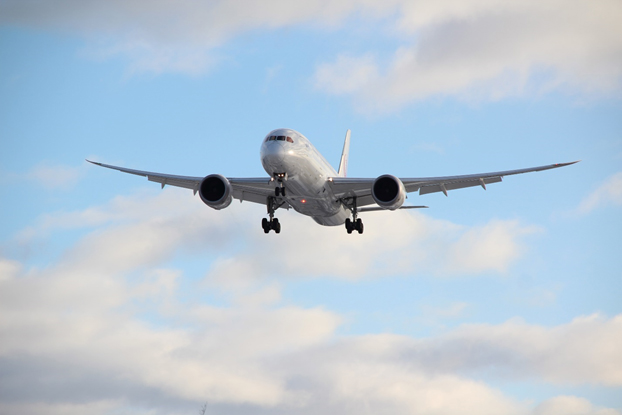
Pic Credits: Unsplash
The story of the exponential growth of the aerospace industry is quite amazing and is well known. The extent of advancement that has been made in the aerospace sector is probably unprecedented in the history of mankind. However, this sector would have made much more progress if the right materials were available to cater to its ever-increasing demands. It would not be wrong to say that one of the major hurdles that are pulling back advancement in the aerospace sector is Materials. This goes a long way in proclaiming the importance of materials in every field associated with us. It is said that the technological advancement made by mankind is large because of the progress made in the field of materials. Materials are everywhere – from a pin to a heart valve, from a pen to the deck of an aircraft carrier. Thousands of materials engineers around the world are toiling hard to provide better materials for every application associated with life and the aerospace sector is one important among them.
Lightweight but strong materials can increase the efficiency of aircraft by several folds in terms of fuel efficiency, higher payload, and flight range, which contribute directly to the operating costs of the aircraft. Materials engineers and scientists have spent their lifetime in developing advanced materials with optimized properties to reduce weight, provide increased damage tolerance, corrosion, and fatigue resistance. The research and development activities in the aerospace sector are not new and it began on the first day of flight itself when air-frames made of wood were used to build aircraft. Later aluminum alloys made a foray into the field of aerospace materials and their dominance is seen even today though the number of new materials being proposed every day is not small. Advanced materials are considered in the aircraft industry for two major applications, aircraft engines, and aircraft structures.
Aluminum-based alloys remain the important air-frame structure materials even to this day given their numerous advantages like lightweight, low cost, and the ability they offer to be manufactured easily. They can be heat treated and used under substantial-high stress level conditions with ease. Among the aluminum alloys, those alloyed with copper, zinc, and lithium are important. Aluminum alloyed with copper is heat treatable and is reported to offer strength that is comparable with steel. Such alloys offer superior damage tolerance and better fatigue resistance than other aluminum alloys. An important member of the aluminum-copper alloy group is the 2024 alloy which is extensively researched as an aircraft fuselage material. Aluminum alloyed with zinc is another category of aluminum alloys and they too are heat treatable to provide the highest strength than any other aluminum-based alloys. Hence alloys of this group are considered for upper wing skin, stringers, and stabilizers where strength requirement is of paramount importance. Lithium is another alloying element that is added to aluminum to reduce its weight. It is found that just the addition of 1% lithium reduces the weight of the aluminum alloy by as much as 3% and most importantly increases Young’s modulus by 6%. Hence, aluminum-lithium alloys are the lightest among all the aluminum alloys. It has been reported that aluminum-lithium alloy when used for fuselage skin and upper wing skin application can provide a weight saving of 7% to 14% by weight.
Magnesium alloys need a special mention when discussing aerospace materials given their lightweight. They are the lightest structural metals available and can reduce the weight of a structure by as much as 33% in comparison with an equal volume of aluminum and by 77% in comparison with an equal volume of steel. Apart from their remarkably low density, magnesium alloys have other advantages too. They can be cast easily, can be recycled, and is available in abundance. When alloyed with elements like aluminum, zinc, zirconium, and a few rare earth elements, they qualify for use in the aerospace industry for various applications. Interestingly, the Sikorsky helicopters use them in gearbox transmissions.
Titanium alloys are another important class of aerospace materials used for both engines and structural applications. They are widely considered for aircraft springs, helicopter rotor systems, and engine compressor parts. The prominent reason for their popularity is their high specific strength, excellent corrosion resistance, and good high-temperature performance. Titanium alloys are of three types namely, alpha, beta, and alpha-beta titanium alloys. Among these, the alpha-beta titanium alloys are the most widely used because of their significant combination of strength, ductility, and fracture toughness. They account for more than 70% of the global titanium market. Ti-6Al-4V is considered the workhorse among this group of titanium alloys. Along with a few more that belong to the same group, these alloys are candidate materials for applications in both aircraft engines and structures including fuselage, landing gears, floor support structures, and compressor discs.
Nickel-based super-alloys are yet another group of materials that have admirable mechanical properties in comparison with stainless steel at temperatures as high as 700°C and can achieve a yield strength that is about 3 times higher. Given their high strength at elevated temperatures, they are increasingly considered for such aircraft engine parts like combustor and turbine sections where the operating temperatures are easily in the range of 1100 and 1250°C.
Despite all the above advantages, the percentage of the alloys used in an aircraft today is on a slight decline with the advent of newer materials especially composite materials. Composite materials are a new class of advanced materials that have revolutionized the engineering materials domain with their exceptional properties. The aerospace sector is heavily inclined towards the usage of composite materials majorly due to their higher specific strength (strength/density) combined with better fatigue and corrosion resistance than that offered by most metal alloys. For instance, carbon fiber reinforced polymer composite materials offer good strength with very low density. The density of these materials is just one-fifth that of steel and three-fifth of aluminum alloys. Ceramic-based composite materials are proved to sustain higher operating temperatures of up to 1400°C which can easily cater to the increasing demand for aircraft speed. Carbon fiber reinforced silicon carbide composite materials are candidate materials for aircraft brakes where temperatures encountered can go up to 1200°C in case of emergency braking situations. The aerospace industry is increasingly considering composite materials for not just structural applications but also some engine parts. Composite materials today contribute to around 25% of the Airbus A380 and 50% of the Boeing 787 aircraft which is quite remarkable and needless to say it is only going to get better with time.
Dr. Girish B. M.
Professor and Head
Department of Mechanical Engineering
Alliance College of Engineering and Design